模具用葉輪的五軸加工中心加工工藝分析
時間:2015-07-17 08:21來源:山東海特數控機床
本文中所用于加工的葉輪是為生產葉輪的模具而制造的葉輪母輪。該母輪被加工完成后,用于加工出硅膠模葉輪,進而再制造出生產產品葉輪的石膏注塑模具,*后使用模具生產出產品葉輪。
文章對模具用葉輪進行了五軸加工中心加工工藝分析,并從加工工藝方面為該葉輪的加工設置了加工工藝路線,詳細介紹了加工工藝路線中半精加工部分存在的問題和該部分問題的重要性。為葉輪加工工藝路線的實用性提供了實際加工依據。
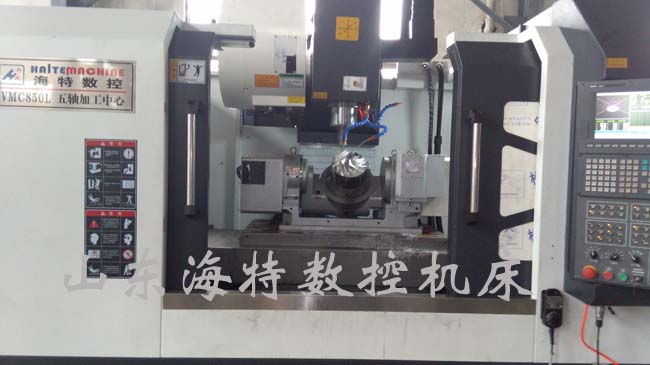
1 整體葉輪結構的工藝分析
在本所用實例中,需要對整體葉輪的流道部分、葉片表面和過渡圓角位置主要曲面進行加工。
并且,在葉片之間的流道部分有大量的多余材料需要去除。為了使葉輪滿足氣動性的要求,葉片常采用大扭角、根部變圓角的結構,這給葉輪的加工提出了*高的要求。根據本例具體情況下面介紹其加工難點。
①要加工的流道變窄,葉片相對較薄且較長,剛度不高,屬于薄壁類零件,加工過程中容易發生變形。
②流道*窄處葉片深度尺寸超過刀具直徑的8倍以上,而相鄰葉片切削空間極小,在加工過渡圓弧時刀具直徑較小,容易使刀具折斷,切削深度的設置也是加工中的關鍵技術。
③本文中整體葉輪葉片曲面為自由曲面,流道較窄,葉片扭曲嚴重,并且有后仰趨勢,加工時易產生刀具干涉,加工難度大。此葉輪由于有分流葉片,為了避免刀具干涉,要分段對曲面加工,因此,保證加工表面精度一致性也是難點。
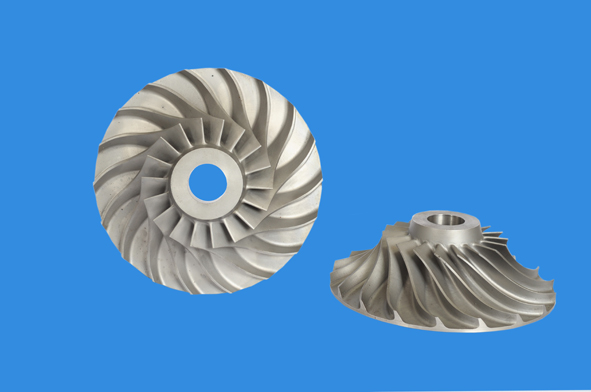
2 葉輪的加工階段劃分的工藝分析
2.1 對毛坯進行基準面的車削加工
由于用于整體葉輪加工的材料多為圓柱棒料,由棒料加工到葉輪外形毛坯會有大量余量需要切除。而粗加工是為了是*快速的切除整體葉輪各個表面的大量多余的材料,加工出葉輪的過渡毛坯和葉輪基本形狀。如果直接使用五軸加工中心和球頭刀來銑削需要大量的時間,加工效率極低。所以使用普通數控車床可以輕松完成對余量的加工。
2.2 在加工葉輪的同一臺五軸加工中心上完成毛坯的外形
精加工
由于在葉輪的加工外形精度要求中,對如圖1中所示的三部分圓柱面的同軸度要求非常高,而經過車床加工的葉輪過渡毛坯又需要再次裝夾到五軸加工中心上,會產生裝夾誤差,難以保證同軸度的要求。因此,需要在粗加工毛坯之后留下余量,另外在加工葉輪用機床上對葉輪過渡毛坯進行精加工,使毛坯的所有外形曲面一次加工成型,以保證同軸度要求。
2.3 葉輪流道的兩次粗加工
由于本文中所用葉輪有分流葉片,而且葉片曲率較大,主葉片與分流葉片間距較小,所以對刀具直徑要求較高。在*初的對流道粗加工的試加工中使用R1A3的球頭刀進行一次完整加工,使用HYPERMILL軟件建立的刀路軌跡如圖2A所示,從圖中可看出刀路軌跡密集,切削層深度小,加工中時間需求較長,加工效率低。
因此,改用R1.5A3球頭刀進行一次完整流道粗加工,但由于分流葉片、葉片曲率和刀具直徑過大的問題,HYPERMILL軟件在計算刀路軌跡時產生了干涉報警,如圖2B所示。在解決了干涉問題后,又出現了無法一次完整粗加工的情況,如圖2C所示。
于是改進了工藝路線,先使用R1.5A3球頭刀進行第一次流道粗加工,再使用R1A3球頭刀對其余毛坯余量進行第二次粗加工。使用HYPERMILL軟件仿真加工如圖2D所示。
這種工藝路線可以大幅度節省加工時間,又可以很好的完成加工的需要。
2.4 葉輪的半精加工
為了降低加工成本,節省加工時間,提高加工的效率,一般首先用大直徑的刀具并使用大的切削量進行快速粗加工。圖3A所示為粗加工后的零件表面。
半精加工的過程是為了去除由于使用的粗加工刀具直徑較大和大的切削量而遺留在零件標準外形之間的材料,或是因為刀具的拐角半徑的存在而遺留在零件壁和底面之間的剩余材料,為了使精加工過程中,零件的加工余量較小,并且*加均勻而進行的加工被稱為半精加工。
在對本文中所使用的葉輪進行試加工的過程中,為了提高生產效率,進行了無半精加工的加工實驗,結果加工出的葉輪葉片厚度尺寸及表面精度達不到成品的要求。問題一為葉片厚度尺寸誤差問題。問題二如圖3B所示為葉輪被加工后表面材料分部不均勻導致的表面粗糙度達不到成品要求。
以上問題出現后,通過查閱資料了解到誤差產生的原因:
①機床主軸轉速不夠高,基于實際加工條件的影響,本文中所用的機床的額定主軸轉速僅為12 000 r/min,而加工中為了保證加工的穩定性,平均使用轉速為10 000 r/min,達不到高速加工的要求。但本文正好可以為非高速加工加工葉輪類零件提供參考經驗。
②在數控機床加工整體葉輪的過程中,機床自身熱誤差和加工系統變形誤差是兩個較重要的誤差原因。機床熱誤差可以通過調控環境溫度,縮短加工周期和使用冷卻液得到一定的補償。加工系統的變形主要有刀具變形和葉片變形。如圖3A所示,粗加工后的葉輪表面毛坯余量殘留高度太大,以及殘留毛坯分布極不均勻,再因為葉片較薄,因此在粗加工后直接進行精加工就會產生葉片厚度尺寸誤差。
③因為通常刀具裝夾方式多為懸臂梁,在整個加工系統中是剛性較薄弱的環節,而且加工葉輪所用的刀具一般細且長,因此刀具的彈性變形是葉輪的加工過程中曲面法向加工誤差產生的一項重要原因。因此,大的毛坯余量殘留及殘留余量分布極不均勻為導致加工后葉輪表面精度達不到成品要求的原因。
基于以上加工失敗的原因,在加工工藝路線制定過程中,加入了半精加工的工藝路線。目的是為了盡量的去除殘留毛坯的數量及高度,使精加工余量盡量減小和使精加工余量的分布*均勻,把毛坯殘留對精加工及刀具的影響降到*低。圖3C所示為半精加工后的葉輪表面。圖3D所示為成品葉輪*終表面。
2.5 葉輪的精加工
精加工是對葉輪的*終加工,此部分內容為所有高精度零件的加工中必不可少缺少的工藝部分,在此不過多描述。
3 結 語
本文以某種模具用葉輪的實際加工為例,通過對該整體葉輪的工藝性研究,有針對性的對加工中的難點分析,繼而制定了該葉輪的加工工藝路線,并從實際加工和使用HYPERMILL軟件對葉輪的加工過程中所遇到的實際問題進行分析,驗證了加工工藝路線的實用性,為葉輪類零件的加工提供實際經驗。文中工藝已應用于葉輪模具的制造,實際價值明顯。